ISO Class 5 Cleanroom: Class 100 Cleanroom Requirements
Cleanrooms: What Are They and How Do They Work?
Cleanrooms (or clean rooms) are rooms with a controlled level of aerosol particles, chemical fumes and other pollutants because of the HEPA filtration that removes particles from the air. A cleanroom is used for manufacturing when there is a need for sterility and cleanliness. It is utilized by medical device manufacturers, pharmaceutical manufacturers, semiconductor manufacturers. Additionally, cleanrooms are used by the food, beverage, e-liquid, CBD, vitamin industries, and many other sub-sectors.
The pharmaceutical industry relies heavily on cleanrooms to manufacture ingredients and products protected from microbiological contamination. Clean rooms are mainly equipped with HEPA filters and, when necessary, ULPA filters and dehumidifiers.
Jump to Section:
Cleanrooms: What Are They and How Do They Work?
About Us – Pristine Clean Bags®
Cleanrooms Classification, Standards and Requirements
What is ISO Class 5 Cleanroom? – Its Classification and Standards
Design Requirements for ISO Class 5 Cleanroom
Mandatory ISO 5 Cleanroom Testing
How Can We Control Particle Levels in a Cleanroom?
How to Control the Contaminant Levels in an ISO 5 Cleanroom?
Cleaning ISO Class 5 Cleanrooms
Depending on the manufacturer’s choice, clean rooms are regulated by government agencies, International Organization for Standardization, or industry standards, and they have to meet ISO 14644, GMP and FDA standards.
About Us – Pristine Cleanroom Bags®
Jarrett Industries has been offering cleanroom bags for over forty years using non-animal, non-surfactant, and virgin materials under controlled conditions. With Pristine Cleanroom Bags®, you can get all the cleanroom packaging you need, from bags to polyethylene film. As a leader in the market, we pride ourselves on our on-time delivery, quality, and customer service.
Our products are produced under certified controlled conditions to minimize contamination risks and comply with FDA requirements. We carry poly tubing, LDPE bag, LDPE tear-resistant bags, HDPE bags, moisture barrier film, and nylon/PE bags.
Contact us today to learn more about Pristine Clean Bags® specifications, bag types, variations, and delivery options.
Cleanrooms Classification, Standards, and Requirements
Cleanrooms must comply with ISO 14644, FDA, and GMP standards. They are classified from ISO 9 to ISO 1 class.
In semiconductor production, biotechnology, and other highly sensitive areas where environmental contamination is a problem, cleanrooms can span thousands square meters.
Here is the graph that shows all ISO 14644-1 cleanroom standards and classifications, as well as FED STD 209 equivalent:
Class | Maximum Particles/m³ | FED STD 209E equivalent | |||||
>0.1 um | >0.2 um | >0.3 um | >0.5 um | >1 um | >5 um | ||
ISO 1 | 10 | 2 | |||||
ISO 2 | 100 | 24 | 10 | 4 | |||
ISO 3 | 1,000 | 237 | 102 | 35 | 8 | Class 1 | |
ISO 4 | 10,000 | 2,370 | 1,020 | 352 | 83 | Class 10 | |
ISO 5 | 100,000 | 23,7000 | 102,000 | 3,520 | 8,320 | 293 | Class 100 |
ISO 6 | 1,000,000 | 237,000 | 102,000 | 35,200 | 8,320 | 2,930 | Class 1,000 |
ISO 7 | 352,000 | 83,200 | 2,930 | Class 10,000 | |||
ISO 8 | 3,520,000 | 832,000 | 29,300 | Class 100,000 | |||
ISO 9 | 35,200,000 | 8,320,000 | 293,000 | Room Air |
What is ISO Class 5 Cleanroom? – Its Classification and Standards
Cleanrooms classified as ISO 5 are extremely clean. The cleanroom must have less than 3,520 particles larger than 0.5 microns per cubic meter and 250-300 HEPA filtered air changes per hour. In other words, the equivalent FED class is 100 particles per cubic foot.
ULPA filtration is 99.9995% effective at 0.12 microns. Common purposes are semiconductor manufacturing and pharmaceutical packing areas.
The following industries frequently use ISO class 5 cleanrooms:
- Life Sciences (Chemistry and Medical Biology)
- Computer & Electronic Part Manufacturing
- Food Manufacturing Industries
- Aerospace Industry
- Biotech Industry
- Nanotechnology
To reach ISO Class 5 air cleanliness in a classified room, one must pass through an ISO 8 (anteroom), an ISO 7, and then an ISO 6 before entering the ISO class 5 cleanroom.
However, you can reach ISO 5 cleanrooms with two or three airlocks. When designing a cleanroom layout, many factors must be considered. For example, the number of people working inside, how much heat the room will generate, and the size of the room.
Moreover, ISO 5 or class 100 cleanrooms need unidirectional airflow. Compared to non-directional airflow cleanrooms, unidirectional airflow cleanrooms use much more air. The whole ceiling is covered in high-efficiency filters.
Filtered air sweeps down the room in a unidirectional manner, at a velocity between 0.3 m/s and 0.5 m/s, with GMP A/B (EU GMP grade standard) also looking at 5.0µ before exiting through the floor, removing all airborne contamination. Cleaning areas that use unidirectional airflow are more expensive compared to directional counterparts. Still, they can comply with rigorous classifications such as ISO 5 or lower.
To achieve ISO Class 5, monobloc and hardwall cleanroom construction is the best option. For example, monobloc is an ideal solution for companies striving for GMP standards and regulations. It accommodates features such as coved floors and interlocked doors.
Design Requirements for ISO Class 5 Cleanroom
Criteria | Class 100 ISO-5 |
Air changes per HR/Min | 300 to 480 / 5 to 8 |
Filter coverage % | 60 – 70 |
CFM per square foot | 36 – 65 |
Filter Efficiency | 99.997% HEPAs |
Ceiling Type | Aluminum T-bar grid |
Light Fixture type | Tear drop or 2’x4’ cleanroom fixture |
Ceiling Panel | FRP, Vinyl rock or Mylar |
Wall System | Modular or standard built |
Flooring cover | Welded sheet vinyl or Epoxy |
Flooring base | Cove or Aluminum base channel |
Air Returns | Low wall on the long axis |
Mandatory ISO 5 Cleanroom Testing
As with other cleanroom classes, ISO 5 cleanrooms must undergo the same testing procedure. Cleanrooms are typically tested and certified after construction is complete to ensure they are built according to specifications.
Testing comprises of airflow test, air pressure cascade and particle count test. It is done according to ISO 14644-1, ISO 14644-2, and ISO 14644-3. These tests can also monitor relative humidity, temperature, lighting, noise, and vibration if needed.
- Airflow: maximum time 6 months, test method ISO 14644-1 Annex B4
- Air Pressure Cascade: maximum time 6 months, test method ISO 14644-1 Annex B5
- Particle Count Test: maximum time 6 months, test method ISO 14644-1 Annex A
How to Control Particle Levels in a Cleanroom?
A cleanroom’s cleanliness is affected by the following factors:
- The design and layout of cleanrooms should incorporate gray zones, associated systems, an air preparation system, and accessories specific to cleanrooms and required by the technology.
- HVAC systems require a calculated number of filter changes, including HEPA and ULPA filters.
- Variable pressure prevents contaminated air from entering a cleanroom (over- and under-pressure).
- Made of easy-to-clean materials that do not produce particles, dirt, or chemicals.
- The staff MUST wear protective clothing when entering the cleanroom.
- Keeping the air in a cleanroom as clean as possible is essential.
- The room should be cleaned with
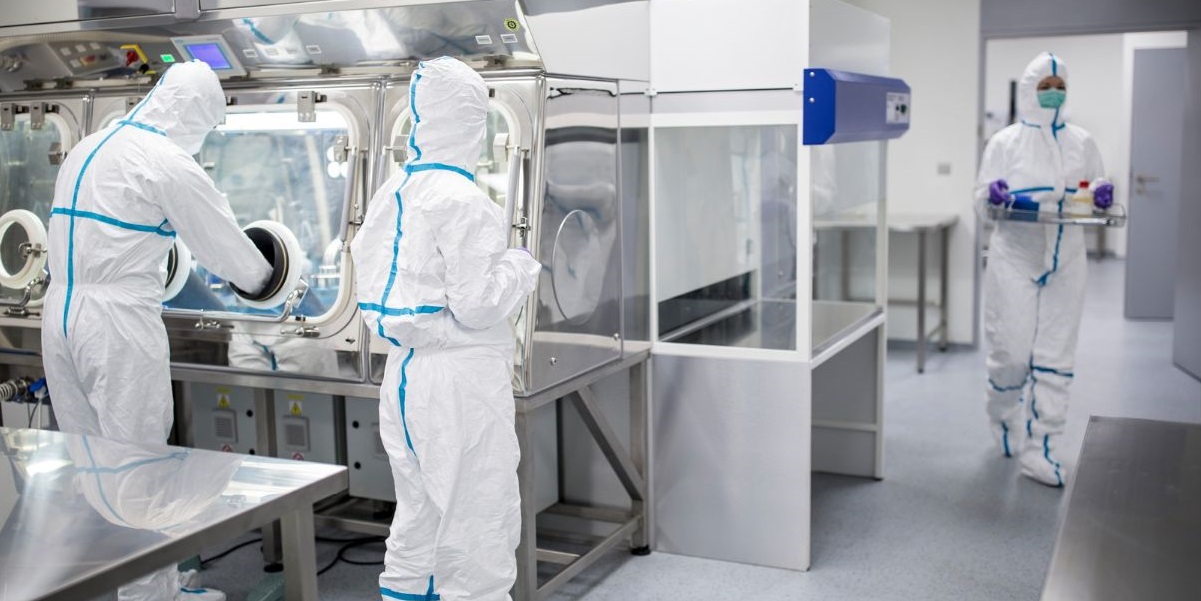
How to Control the Contaminant Levels in an ISO 5 Cleanroom?
It can be challenging to keep the contaminant level low in a cleanroom, but here’s what everyone can do to control it:
- Don’t go straight into the cleanroom after smoking
- Wash clothes before entering and after leaving
- Wash hands before and after leaving
- Do not bring needless equipment
- Cover hair/beard with a hairnet
- Move slowly and calmly
- Talk as little as possible
Cleaning ISO Class 5 Cleanrooms
Cleanliness is achieved through a higher level of filtration. Cleaning should be done daily or weekly, depending on the job’s demands. Take a look at the cleaning process here:
Weekly Cleaning
- The walls should be cleaned with distilled water and a wet sponge and then vacuum dried.
- Mop and vacuum the floors with distilled water and cleanroom detergent.
Daily Cleaning
- Put away products between shifts to prevent further contamination.
- Mop the floors and vacuum them prior to starting your shift.
- Clean and dry both the window and passthrough.
- Vacuum the walls using a HEPA vacuum.
- Clean your work area after every shift.
Looking for Cleanroom Packaging Solution? Look No Further Than Pristine Clean Bags®
We’re the right choice if you’re looking for the most trustworthy ISO 5 cleanroom supplier. Our ISO-certified cleanroom bags meet various industry requirements, and our bags are compliant with FDA and ISO standards. We can offer competitive pricing on US and EU markets because we have access to unique sourcing capabilities. On-time delivery, outstanding quality, and exceptional customer service are our promises.
You may contact us via email or call (410) 581-0303.
You May Also Find Interesting:
- ESD Bag vs. Anti-Static Bag: What is the Difference and What is the Best Choice for Your Cleanroom Needs
- Clean Room Packaging: A Key to Avoiding Contamination and Ensuring Product Quality
- Cleanroom 101: Definition, History, Uses and ISO Cleanroom Requirements
- Why is Pristine Clean Bags® Ideal Clean Room Packaging Supplier in 2022?
- Controlled Environment vs. Cleanroom: Key Differences
- 4 Essential Things to Know About Cleanroom Bag