ISO 7 Cleanroom : Class 10,000 Cleanroom Requirements
What Are Cleanrooms?
A cleanroom is an environment with a low number of pollutants such as dust, aerosol particles and chemical fumes. Clean rooms have a controlled level of pollution defined by the number of particles per cubic meter in a specific size. The ambiance in a typical urban environment contains 35,000,000 particles per cubic meter of 0.5 μm and more, meeting the ISO 9 cleanroom standard. In comparison, ISO 1 cleanroom allows 0 particles in that size range, 12 particles per cubic meter of 0.3 μm and less.
In the pharmaceutical industry, clean rooms play a key role in producing ingredients and products that need to be protected from microbiological or any other contamination. These cleanrooms are mainly equipped with HEPA and, if necessary, ULPA filters and dehumidifiers. Thus, implementing cleanrooms is one way to control contaminants.
Cleanrooms must comply with GMP, FDA, and ISO 14644 standards. Compliance with applicable regulations in cleanroom technology allows its application of classes from ISO 9 to ISO 1.
Cleanrooms are either regulated by governmental agencies or regulated by industry standards. It is up to the manufacturer to determine which laws and standards apply to them. Medical device manufacturers commonly demand ISO 7 and ISO 8 cleanrooms.
Pharmaceutical, electronic, and medical device manufacturers are most likely to use ISO 7 cleanrooms.
Pristine Clean Bags® – ISO 7 Cleanroom Supplier
Jarrett Industries have been serving cleanroom facilities with cleanroom products for more than four decades. Our cleanroom packaging has everything needed to meet your business needs. Our products are manufactured under certified and controlled conditions, only using virgin resins to minimize contamination risk and comply with FDA and EU regulations. As a renewed cleanroom packaging supplier, we are proud to lead the flex packaging industry in quality, customer service, and on-time delivery. We supply cleanroom poly tubing, moisture-barrier film, nylon/PE bags, LDPE easy-tear bags, HDPE bags, and LDPE bags.
Contact us today to learn more about Pristine Clean Bags® specifications, bags type, variations, delivery options and prices.
Cleanroom Requirements
Cleanrooms can be very large. The entire production can be located inside thousands of square meters of clean rooms. They are intensively used in semiconductor production, biotechnology and other areas that are very sensitive to environmental contamination.
The air entering the cleanroom from the outside is filtered to remove dust, and the air inside is constantly recirculated through high-efficiency air filters to remove internally generated pollution.
Staff enters and leaves clean rooms through air chambers (which sometimes contain air showers) and wear protective clothing such as hoods, face masks, aprons, gloves, boots, gowns, hairnets, shoe covers, lab coats, and capes.
It is important to mention that cleanrooms are not sterile but extra clean without uncontrolled microbes. In that way, only airborne particles are controlled.
Some cleanrooms are kept under positive pressure so that air leaks out of the room instead of unfiltered air entering the room. In cleanrooms whose air purity standards are not too strict, the entrance to the room does not have to have an air shower. Still, there is an anteroom (known as the “gray room”), where clothes are cleaned and from which a cleanroom is entered directly.
To read more about cleanrooms – types, uses, designs and requirements, visit this guide.
Cleanroom Classification and Standards
In the US and Canada, cleanrooms are classified according to the cleanliness of the air. The cleanroom classification system ISO 14644-1 is the level of cleanliness the room meets, determined by the size and quantity of particles per air volume.
Among these standards are the cleanroom classes ISO 1, ISO 2, ISO 3, ISO 4, ISO 5, ISO 6, ISO 7, ISO 8 and ISO 9, ISO 1 being the “cleanest” and ISO 9 the dirtiest (yet still cleaner than a standard room). ISO 7 and ISO 8 are the most common classes.
Cleanrooms are classified by the amount and size of particles per air volume, measured in micrometers (m). Standard cleanrooms are based on particle size or microns (m).
Some cleanroom classifications do not require certain particle sizes due to low or high concentrations of particles equal to or larger than those shown below.
Class | Maximum Particles/m³ | FED STD 209E equivalent | |||||
>0.1 um | >0.2 um | >0.3 um | >0.5 um | >1 um | >5 um | ||
ISO 1 | 10 | 2 | |||||
ISO 2 | 100 | 24 | 10 | 4 | |||
ISO 3 | 1,000 | 237 | 102 | 35 | 8 | Class 1 | |
ISO 4 | 10,000 | 2,370 | 1,020 | 352 | 83 | Class 10 | |
ISO 5 | 100,000 | 23,7000 | 102,000 | 3,520 | 8,320 | 293 | Class 100 |
ISO 6 | 1,000,000 | 237,000 | 102,000 | 35,200 | 8,320 | 2,930 | Class 1,000 |
ISO 7 | 352,000 | 83,200 | 2,930 | Class 10,000 | |||
ISO 8 | 3,520,000 | 832,000 | 29,300 | Class 100,000 | |||
ISO 9 | 35,200,000 | 8,320,000 | 293,000 | Room Air |
ISO 7 Cleanroom Requirements
An ISO 7 cleanroom is a common cleanroom classification. They are used in biotechnology, pharmaceuticals, nanotechnology, compounding, medical devices, films, ion lithium batteries, packaging, food packages, and nutraceuticals. Class 7 rooms are also called class 10,000 cleanrooms.
Cleanroom regulations stipulate that a cleanroom class 7 should have less than 352,000 microscopic particles per cubic meter and 60 air changes per hour with HEPA filters.
As in the other cleanrooms, multiple outdoor air filters filter and cool the air with progressively finer filters to exclude dust.
Bypassing the air through HEPA filters more often, fewer particles are left in the air. The number of air alterations per hour is determined by dividing the volume of filtered air by the room size in an hour.
An HVAC cleanroom expert should tally the demands of a room because many things must be considered (the size of the room, the number of people in the room, the equipment in the room).
ISO 7 Cleanroom Design
Class 10,000 cleanroom design depends on the application, and here is the most common specification:
- Air return design – low wall
- Ceiling – vinyl rock or Mylar
- Flooring base – aluminum base or cove
- Flooring cover – usually vinyl or VCT
- Wall system – Modular or drywall
- Light fixture type – 2’x4′ cleanroom fixture
Other design features include door types, window positioning, glass walls, Wi-Fi access, security cameras, and intercom and phone devices.
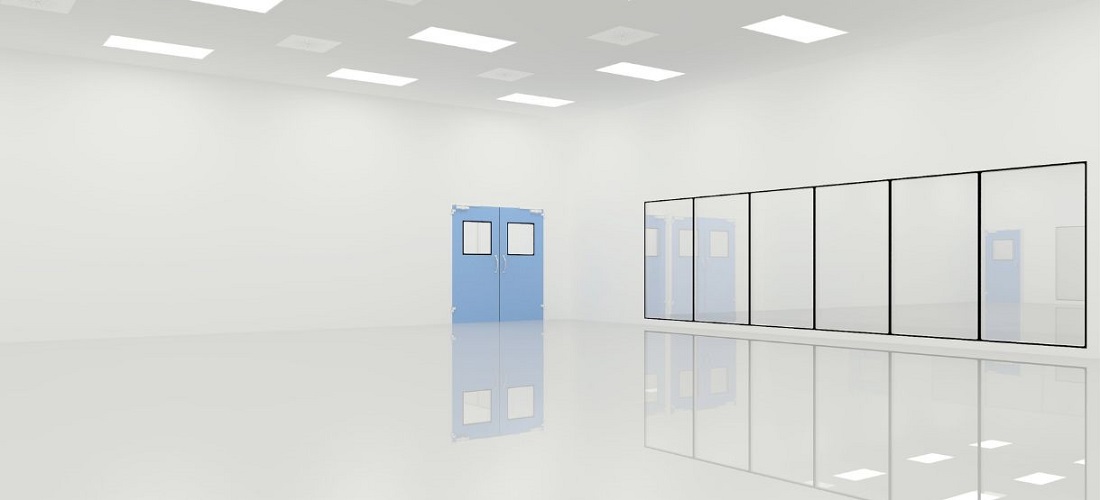
ISO 7 vs. ISO 8 (Class 10,000 vs Class 100,000)
Cleanroom classes differ primarily in the number of air changes per hour they require. This is how many times the air in the system is filtered through HEPA filters. Cleanrooms of ISO Class 8 typically undergo 10-25 air changes each hour, while ISO Class 7 cleanrooms undergo between 30-60 changes each hour. As a result, the air in ISO Class 7 cleanroom is filtered thirty times an hour at least. Air in cleanrooms used for the production of medical devices is consistently filtered to remove particles.
Additionally, cleanrooms are classified according to how many particles are present in the air. There are ten times fewer particles in each class compared to the one above it. An ISO 8 cleanroom can have 100,000 particles per square foot of air, whereas an ISO 7 cleanroom can have 10,000. (terminology related to Federal Standard 209)
How to Control the Level of Particles in ISO 7 Cleanroom?
Things that affect the cleanliness of a cleanroom:
- First, cleanrooms MUST be made of materials that are easy to clean and do not generate dirt, particles, or chemicals.
- Design and layout of cleanrooms should be with gray zones, associated systems, air preparation system, tool connections and other equipment required by the project.
- Equipment in a cleanroom must be designed to allow minimal air contamination. Furniture for cleanrooms must be designed to create minimal particles and be easy to clean.
- The HVAC system (pressure – exhaust – recirculation) must have a well-calculated number of changes and be equipped with filters for good cleanings, such as HEPA or ULPA.
- When the pressure varies (overpressure/under pressure), it prevents contaminated air from entering a cleanroom.
- Staff enters and exits cleanrooms through vents wear protective clothing such as hats, face masks, gloves, shoes, and coveralls, depending on the classification of the cleanroom. Operator-generated contamination accounts for 70% to 80% of cleanroom contamination.
- Clean the room with disinfectant.
Containment and Filtration
- The final filtration step of High-Efficiency Penetration Air (HEPA) Filtration is generally performed at the air entry point of the cleanroom. This can be accomplished by terminal HEPA modules or fan filter modules (HEPA FFU) depending on the application.
- The requirements of a process in the cleanroom drive factors such as temperature, humidity, lighting, noise, static control, and outgassing levels.
- Measuring particle sizes less than 5.0 but greater than 0.
- Particles per cubic meter: 352,000 at 0.5.
ISO Class 7 Cleanroom Cleaning Procedure
The cleanroom should be cleaned daily or weekly. It depends on the job’s requirements and needs. Here is what a cleaning procedure looks like.
Daily Cleaning:
- Use a HEPA vacuum to clean all walls.
- After every shift, clean all work areas.
- All window and pass-through surfaces should be washed and dried.
- Before starting your shift, mop the floors, then vacuum them to dry.
- To prevent further contamination of products, put them away between shifts.
Weekly Cleaning:
- Walls should be cleaned with distilled water and a damp sponge, then vacuum dried.
- Use a cleanroom-specific detergent and distilled water to mop the floors, and vacuum with a HEPA filter.
How to Test and Certify a Class 7 Cleanroom?
Testing ISO 7 cleanroom requires the same procedure as other cleanroom classes. In most cases, the cleanroom undergoes tests and certification after construction is complete to ensure that it was built according to the specifications. The cleanroom is re-tested every 6 or 12 months to ensure that the quality of operation has not changed.
Testing includes airflow test, air pressure cascade and particle count test. Testing is done according to ISO 14644-1, ISO 14644-2, and ISO 14644-3. Depending on cleanroom use and processes, tests may monitor relative humidity, noise, temperature, lighting, and vibration.
Need Packaging for Your Class 7 Cleanroom? Pristine Clean Bags® Can Help
We are the right choice if you look for the best and most trusted ISO 7 cleanroom supplier. Except for medical research, development, pharmaceutical manufacturing and medical device manufacturing, our ISO-certified cleanroom bags meet the requirements of a broad array of industries. We comply with ISO and FDA standards and regulations. Pristine Clean Bags can offer competitive pricing on US and EU markets due to our unique sourcing ability. We promise to deliver superior quality, outstanding customer service, and on-time delivery.
For more information, please send us an email or give us a call at (410) 581-0303.
Related to ISO 7 Cleanroom:
- Cleanroom Validation Protocols in a Nutshell
- Controlled Environment vs. Cleanroom: Key Differences
- 4 Essential Things to Know About Cleanroom Bag
- HDPE vs. LDPE: Understanding the Similarities and Differences
- A Vital Connection Between Contamination Control and Product Quality
- 5 Cleanroom Supplies to Add to Your List
- Why is Pristine Clean Bags® Ideal Clean Room Packaging Supplier in 2022?