Controlled Environment vs. Cleanroom: Key Differences
Although the terms cleanroom and controlled environment are used interchangeably, they refer to different concepts in the contamination control industry. While they do share some characteristics, they differ in some crucial aspects we’ll mention later in the article.
Industries that face high contamination levels must reduce or eliminate airborne particles, dust, and vapor from their workspace to prevent their product from being exposed to contaminants. The part of that process includes either a cleanroom or a controlled environment, depending on the project you’re working on. Additionally, it’s vital to ensure your staff follows the protocols and uses protective equipment to avoid contaminating the area.
Jump to Section
What is a Controlled Environment?
Common Controlled Environment Applications
What is a Cleanroom Environment?
Controlled Environment vs. Cleanroom Environment
How to Choose Between a Cleanroom and a Controlled Environment?
Understanding Cleanroom Classifications
Equipment Necessary for Controlled Environments and Cleanrooms
How to Prevent Contamination of a Cleanroom or a Controlled Environment?
Pristine® Clean Bags: High-Quality Supplies for Cleanrooms and Controlled Environments
Pristine® Clean Bags is your ally in keeping your products safe from contamination even when they leave a cleanroom or a controlled environment. Our cleanroom poly bags are produced in a controlled environment and feature virgin and surfactant-free materials without elements of animal origin.
We are a leading cleanroom packaging supplier that guarantees the highest level of traceability and conformance. Our products are FDA- and EU-compliant and are suitable for a broad range of electronic, medical, pharmaceutical, automotive, and aerospace applications.
What is a Controlled Environment?
A controlled environment, also known as a “critical environment,” is a space that determines parameters to regulate factors such as air pressure, dust, humidity, and temperature. At the same time, it separates personnel from others inside a facility. Companies that apply controlled environment strategies aim to limit human traffic and wear specific protective clothing inside the area.
Operations that implement controlled environments are not required to measure airborne particles and regulate their amount. Instead, HEPA filters are regularly monitored and replaced more frequently than in other industries.
In the case of a controlled environment, workers and visitors may implement procedures to ensure no contamination enters the space. But essentially, the levels of particulate contamination allowed in the controlled environment are not of vital importance.
Common Controlled Environment Applications
A controlled environment room is convenient for many uses, including secret government installations, PPE (Personal Protective Equipment) for the COVID-19 pandemic, and applications involving hemp production and growth.
What is a Cleanroom Environment?
A cleanroom is a space designed to measure, control, and remove contaminants like dust, mold, and microorganisms. Cleanrooms are classified by the maximum number of particles (by size) allowed in the air per cubic meter, and unlike controlled environments, these areas must meet more stringent requirements in terms of temperature and pressure control. For that reason, cleanrooms use industrial HEPA filtration and specialized HVAC systems to filter the air and deliver a contaminant-free environment.
Common Cleanroom Applications
Cleanrooms are commonly used by defense contractors and space institutions, as well as notable companies developing vaccines and pharmaceuticals that need a particle-free environment for sensitive product manufacturing.
A few most common cleanroom applications include, but are not limited to the following:
- Medical device manufacturing and packaging
- Pharmaceutical applications
- Semiconductor production
- Automotive parts production
- Aerospace applications
- Electronic device manufacturing
- Industrial purposes
- Life science and chemical labs
Controlled Environment vs. Cleanroom Environment
The main difference between a cleanroom and a controlled environment is the way the area is regulated. While controlled environments are focused on atmospheric factors such as temperature, air pressure, and humidity levels, cleanroom regulations go a step further. Namely, they employ decontamination and filtration protocols to make the area more strictly regulated than a controlled environment.
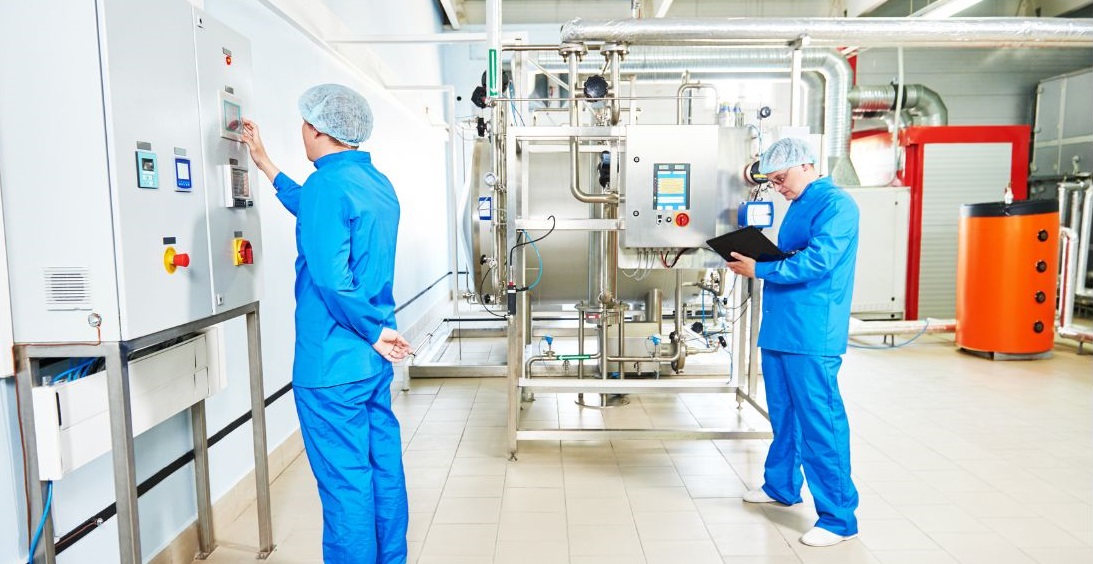
How to Choose Between a Cleanroom and a Controlled Environment?
Not all projects and applications require the same working space. That said, it’s essential to learn whether your processes, machinery, or staff can benefit from a controlled environment or cleanroom conditions.
If your specific application requires a controlled and stable environment with a certain humidity or temperature level, a controlled environment is a way to go. On the other hand, you’ll need a cleanroom when your industry entails a particular decontamination or filtration level to make sure that the manufacturing process is conducted in a safe environment free from airborne particles.
Understanding Cleanroom Classifications
Any cleanroom environment is classified based on the level of cleanliness inside the area, which is determined according to the number and size of particles per cubic meter of air. The ISO Classification system ISO 14644-1 is a leading authority in the US and Canada, and cleanrooms must follow its protocols to ensure a safe and contaminant-free environment for the product manufacturing process.
The ISO standard refers to the cleanroom classes ranging from ISO 1 to ISO 9. While ISO 1 is considered the “cleanest” class, ISO 9 is observed as the “dirtiest” class. However, it is much cleaner than a regular room.
Let’s consult the chart below to understand the ISO standards better:
Class | Maximum Particles/m³ | FED STD 209E equivalent | |||||
>0.1 um | >0.2 um | >0.3 um | >0.5 um | >1 um | >5 um | ||
ISO 1 | 10 | 2 | |||||
ISO 2 | 100 | 24 | 10 | 4 | |||
ISO 3 | 1,000 | 237 | 102 | 35 | 8 | Class 1 | |
ISO 4 | 10,000 | 2,370 | 1,020 | 352 | 83 | Class 10 | |
ISO 5 | 100,000 | 23,7000 | 102,000 | 3,520 | 8,320 | 293 | Class 100 |
ISO 6 | 1,000,000 | 237,000 | 102,000 | 35,200 | 8,320 | 2,930 | Class 1,000 |
ISO 7 | 352,000 | 83,200 | 2,930 | Class 10,000 | |||
ISO 8 | 3,520,000 | 832,000 | 29,300 | Class 100,000 | |||
ISO 9 | 35,200,000 | 8,320,000 | 293,000 | Room Air |
Any class greater than an ISO Class 8 is considered a controlled environment, while anything less than that often requires additional decontamination and filtration.
It’s vital to understand that not all industries operate in the same ISO Class environment. For instance, if you’re packaging medical devices, you’ll probably need an ISO Class 7 or even higher-class cleanroom. On the other hand, companies dedicated to chrome plating are not required to meet specific ISO classifications but must provide a controlled environment.
In some situations, you may need to provide both a controlled environment and a cleanroom to meet your industry’s specific needs. A controlled environment will be necessary for sensitive materials, while an ISO-certified cleanroom is essential for quality control testing.
Equipment Necessary for Controlled Environments and Cleanrooms
You might operate in a highly controlled environment or cleanroom with the strictest cleanliness standards, but individuals who enter and exit the area carry potential particles and contaminants on their skin, hair, and clothing. Therefore, your team may inadvertently put your cleanroom environment at risk of particle contamination, potentially affecting your product quality and manufacturing process.
To prevent that, it’s quintessential to provide adequate cleanroom supplies and protective equipment that ensure particle control. For instance:
- Cleanroom packaging supplies
- Cleanroom protective garments (gowns, gloves, face masks, shoe covers, boots, etc.)
- Cleanroom furniture
- Cleaning materials (buckets, mops, vacuum cleaners, wipes, detergents, etc.)
- Airflow devices to minimize dus
- Special containment walls and plastics
- Adequate air filtration systems
- Temperature and humidity controls
- Airlocks and decontamination areas
- Disposable personal protective equipment (PPE)
How to Prevent Contamination of a Cleanroom or a Controlled Environment?
The first step towards keeping your cleanroom space safe from contaminants and airborne particles is ensuring that the people entering and leaving a cleanroom have undergone contamination control awareness and training.
Before entering a cleanroom or a controlled environment, personnel should decontaminate and wear protective garments such as face masks, lab coats, foot coverings, protective overalls, etc. In case you work in stringent cleanrooms, your staff must go through decontamination to eliminate the risk of releasing biohazards into the public when exiting.